Laserové svařování v posledních letech díky rychlému rozvoji nové energetiky rychle proniklo do celé nové energetiky pro své rychlé a stabilní přednosti. Mezi nimi laserová svářecí zařízení představují nejvyšší podíl aplikací v celém novém energetickém průmyslu.
Laserové svařováníse rychle stal první volbou ve všech oblastech života díky své vysoké rychlosti, velké hloubce a malé deformaci. Od bodových svarů po tupé svary, návarové a těsnící svary,laserové svařováníposkytuje bezkonkurenční přesnost a kontrolu. Hraje důležitou roli v průmyslové výrobě a výrobě, včetně vojenského průmyslu, lékařské péče, letectví, 3C autodílů, mechanických plechů, nové energetiky a dalších průmyslových odvětví.
Ve srovnání s jinými technologiemi svařování má laserové svařování své jedinečné výhody a nevýhody.
Výhoda:
1. Vysoká rychlost, velká hloubka a malá deformace.
2. Svařování lze provádět při normální teplotě nebo za zvláštních podmínek a svařovací zařízení je jednoduché. Například laserový paprsek se nepohybuje v elektromagnetickém poli. Lasery mohou svařovat ve vakuu, vzduchu nebo určitých plynných prostředích a mohou svařovat materiály, které jsou přes sklo nebo propustné pro laserový paprsek.
3. Může svařovat žáruvzdorné materiály, jako je titan a křemen, a také může svařovat různé materiály s dobrými výsledky.
4. Po zaostření laseru je hustota výkonu vysoká. Poměr stran může dosáhnout 5:1 a při svařování vysoce výkonných zařízení může dosáhnout až 10:1.
5. Lze provádět mikrosvařování. Po zaostření laserového paprsku lze získat malý bod, který lze přesně umístit. Může být aplikován na montáž a svařování mikro a malých obrobků pro dosažení automatizované hromadné výroby.
6. Dokáže svařovat těžko přístupná místa a provádět bezkontaktní svařování na dlouhé vzdálenosti s velkou flexibilitou. Zejména v posledních letech technologie laserového zpracování YAG přijala technologii přenosu optických vláken, která umožnila širší propagaci a aplikaci technologie laserového svařování.
7. Laserový paprsek lze snadno rozdělit v čase a prostoru a více paprsků může být zpracováno na více místech současně, což poskytuje podmínky pro přesnější svařování.
Přeběhnout:
1. Požaduje se vysoká přesnost montáže obrobku a poloha paprsku na obrobku nemůže být výrazně vychýlena. Je to proto, že velikost laserového bodu po zaostření je malá a svar je úzký, což ztěžuje přidávání přídavných kovových materiálů. Pokud přesnost montáže obrobku nebo přesnost polohování paprsku neodpovídá požadavkům, jsou náchylné ke vzniku vad svařování.
2. Náklady na lasery a související systémy jsou vysoké a jednorázová investice je velká.
Běžné vady laserového svařováníve výrobě lithiových baterií
1. Pórovitost svařování
Běžné závady vlaserové svařováníjsou póry. Svařovací tavenina je hluboká a úzká. Během procesu laserového svařování proniká dusík do roztavené lázně zvenčí. Během procesu ochlazování a tuhnutí kovu klesá rozpustnost dusíku s poklesem teploty. Když se roztavený kov v bazénu ochladí a začne krystalizovat, rozpustnost prudce a náhle klesne. V této době se vysráží velké množství plynu a vytvoří bubliny. Pokud je rychlost plovoucí bubliny menší než rychlost krystalizace kovu, vytvoří se póry.
V aplikacích v průmyslu lithiových baterií často zjišťujeme, že póry se zvláště pravděpodobně vyskytují během svařování kladné elektrody, ale zřídka se vyskytují během svařování záporné elektrody. Je to proto, že kladná elektroda je vyrobena z hliníku a záporná elektroda je vyrobena z mědi. Během svařování tekutý hliník na povrchu zkondenzuje, než vnitřní plyn zcela přeteče, což zabraňuje přetékání plynu a vytváření velkých a malých otvorů. Malé průduchy.
Kromě výše uvedených příčin vzniku pórů mezi póry patří také venkovní vzduch, vlhkost, povrchová mastnota atd. Navíc na tvorbu pórů ovlivní i směr a úhel foukání dusíku.
Jak snížit výskyt svařovacích pórů?
Za prvé, předtímsvařováníolejové skvrny a nečistoty na povrchu vstupních materiálů je třeba včas vyčistit; při výrobě lithiových baterií je základním procesem vstupní kontrola materiálu.
Za druhé, průtok ochranného plynu by měl být upraven podle faktorů, jako je rychlost svařování, výkon, poloha atd., a neměl by být ani příliš velký, ani příliš malý. Tlak ochranného pláště by měl být nastaven podle faktorů, jako je výkon laseru a poloha zaostření, a neměl by být ani příliš vysoký, ani příliš nízký. Tvar trysky ochranného pláště by měl být upraven podle tvaru, směru a dalších faktorů svaru tak, aby ochranný plášť mohl rovnoměrně pokrývat oblast svařování.
Za třetí, kontrolujte teplotu, vlhkost a prach ve vzduchu v dílně. Okolní teplota a vlhkost ovlivní obsah vlhkosti na povrchu podkladu a ochranného plynu, což následně ovlivní tvorbu a únik vodní páry v roztavené lázni. Pokud je okolní teplota a vlhkost příliš vysoká, bude na povrchu podkladu a ochranného plynu příliš mnoho vlhkosti, což vytváří velké množství vodní páry, což má za následek vznik pórů. Pokud je okolní teplota a vlhkost příliš nízká, bude na povrchu substrátu a v ochranném plynu příliš málo vlhkosti, což sníží tvorbu vodní páry, a tím sníží póry; nechat kvalitní personál zjistit cílovou hodnotu teploty, vlhkosti a prachu na svařovací stanici.
Za čtvrté, metoda houpání paprsku se používá ke snížení nebo odstranění pórů při svařování laserem s hlubokým průnikem. V důsledku přidání švihu při svařování způsobuje vratný výkyv nosníku ke svaru opakované přetavování části svarového švu, což prodlužuje dobu setrvání tekutého kovu ve svarové lázni. Vychýlení paprsku zároveň zvyšuje tepelný příkon na jednotku plochy. Poměr hloubky a šířky svaru je snížen, což vede k tvorbě bublin, čímž se eliminují póry. Na druhé straně, výkyv paprsku způsobí, že se malý otvor odpovídajícím způsobem rozkývá, což může také poskytnout míchací sílu pro svařovací lázeň, zvýšit konvekci a míchání svarové lázně a mít příznivý účinek na odstranění pórů.
Za páté, frekvence pulzů, frekvence pulzů se týká počtu pulzů emitovaných laserovým paprskem za jednotku času, které ovlivní přívod tepla a akumulaci tepla v roztavené lázni a poté ovlivní teplotní pole a proudové pole v roztavené lázni. bazén. Pokud je frekvence pulzů příliš vysoká, povede to k nadměrnému přívodu tepla do roztavené lázně, což způsobí, že teplota roztavené lázně bude příliš vysoká, produkují se kovové páry nebo jiné prvky, které jsou při vysokých teplotách těkavé, což má za následek vznik pórů. Pokud je frekvence pulzů příliš nízká, povede to k nedostatečné akumulaci tepla v tavné lázni, což způsobí, že teplota tavné lázně bude příliš nízká, což sníží rozpouštění a únik plynu, což má za následek vznik pórů. Obecně řečeno, frekvence pulzů by měla být zvolena v rozumném rozsahu na základě tloušťky substrátu a výkonu laseru a neměla by být příliš vysoká nebo příliš nízká.
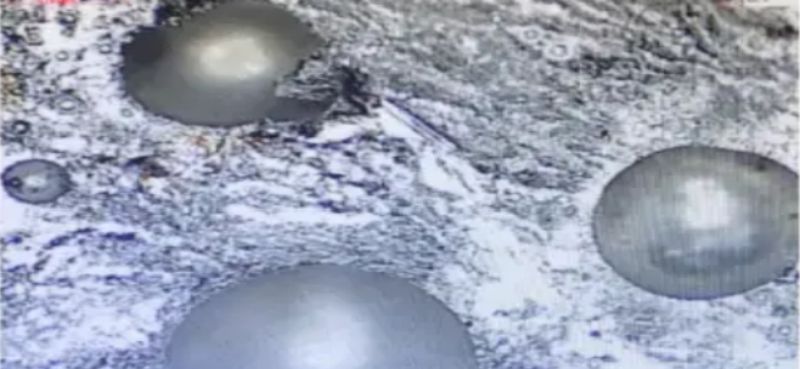
Svařovací otvory (laserové svařování)
2. Svařte rozstřik
Rozstřik, který vzniká během procesu svařování, laserového svařování vážně ovlivní kvalitu povrchu svaru a znečišťuje a poškozuje čočku. Obecný výkon je následující: po dokončení laserového svařování se na povrchu materiálu nebo obrobku objeví mnoho kovových částic a přilnou k povrchu materiálu nebo obrobku. Nejintuitivnější výkon spočívá v tom, že při svařování v režimu galvanometru budou po určité době používání ochranné čočky galvanometru na povrchu husté důlky a tyto důlky jsou způsobeny rozstřikem při svařování. Po dlouhé době je snadné zablokovat světlo a nastanou problémy se svařovacím světlem, což má za následek řadu problémů, jako je přerušené svařování a virtuální svařování.
Jaké jsou příčiny stříkání?
Za prvé, hustota výkonu, čím větší je hustota výkonu, tím snazší je generovat rozstřik a rozstřik přímo souvisí s hustotou výkonu. To je stoletý problém. Přinejmenším zatím průmysl nedokázal problém rozstřikování vyřešit a lze jen konstatovat, že došlo k jeho mírnému omezení. V průmyslu lithiových baterií je šplouchání největším viníkem zkratu baterie, ale nedokázalo vyřešit hlavní příčinu. Dopad rozstřiku na baterii lze pouze snížit z hlediska ochrany. Například kolem svařovací části je přidán kruh otvorů pro odstraňování prachu a ochranné kryty a v kruzích jsou přidány řady vzduchových nožů, aby se zabránilo dopadu rozstřiku nebo dokonce poškození baterie. Zničením prostředí, produktů a komponentů v okolí svařovací stanice lze říci, že byly vyčerpány prostředky.
Pokud jde o řešení problému rozstřiku, lze pouze říci, že snížení svařovací energie pomáhá snížit rozstřik. Snížení rychlosti svařování může také pomoci, pokud je průvar nedostatečný. Ale v některých speciálních procesních požadavcích to má malý účinek. Je to stejný proces, různé stroje a různé šarže materiálů mají zcela odlišné svařovací účinky. Proto v nové energetice platí nepsané pravidlo, jeden soubor parametrů svařování pro jeden kus zařízení.
Za druhé, pokud povrch zpracovávaného materiálu nebo obrobku není vyčištěn, olejové skvrny nebo znečišťující látky také způsobí vážné potřísnění. V této době je nejjednodušší vyčistit povrch zpracovávaného materiálu.
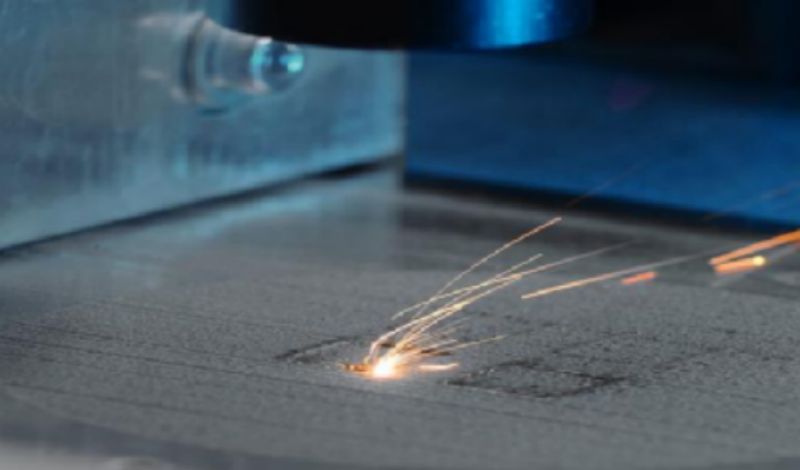
3. Vysoká odrazivost laserového svařování
Obecně řečeno, vysoká odrazivost se týká skutečnosti, že zpracovávaný materiál má malý odpor, relativně hladký povrch a nízkou míru absorpce pro blízké infračervené lasery, což vede k velkému množství laserové emise, a protože se používá většina laserů ve svislém směru Kvůli materiálu nebo malému sklonu se vrací zpět do výstupní hlavy vracející se laserové světlo a dokonce část zpětného světla je připojena k vláknu pro přenos energie a je přenášena zpět podél vlákna dovnitř laseru, což způsobuje, že jádrové komponenty uvnitř laseru mají i nadále vysokou teplotu.
Pokud je odrazivost při laserovém svařování příliš vysoká, lze použít následující řešení:
3.1 Použijte antireflexní povlak nebo ošetřete povrch materiálu: potažení povrchu svařovacího materiálu antireflexním povlakem může účinně snížit odrazivost laseru. Tento povlak je obvykle speciální optický materiál s nízkou odrazivostí, který energii laseru absorbuje, místo aby ji odrážel zpět. U některých procesů, jako je svařování sběračů proudu, měkké spojování atd., může být povrch také ražen.
3.2 Nastavení úhlu svařování: Nastavením úhlu svařování může laserový paprsek dopadnout na svařovaný materiál pod vhodnějším úhlem a snížit výskyt odrazů. Obvykle je dobrý způsob, jak snížit odrazy, mít laserový paprsek dopadající kolmo na povrch svařovaného materiálu.
3.3 Přidání pomocného absorbentu: Během procesu svařování se do svaru přidá určité množství pomocného absorbentu, jako je prášek nebo kapalina. Tyto absorbéry absorbují laserovou energii a snižují odrazivost. Vhodný absorbent je třeba vybrat na základě konkrétních svařovacích materiálů a aplikačních scénářů. V průmyslu lithiových baterií je to nepravděpodobné.
3.4 Použití optického vlákna pro přenos laseru: Pokud je to možné, lze optické vlákno použít k přenosu laseru do svařovací polohy, aby se snížila odrazivost. Optická vlákna mohou vést laserový paprsek do oblasti svařování, aby nedocházelo k přímému vystavení povrchu svařovaného materiálu a ke snížení výskytu odrazů.
3.5 Nastavení parametrů laseru: Nastavením parametrů, jako je výkon laseru, ohnisková vzdálenost a průměr ohniska, lze řídit distribuci laserové energie a snížit odrazy. U některých reflexních materiálů může být snížení výkonu laseru účinným způsobem snížení odrazů.
3.6 Použití rozdělovače paprsku: Dělič paprsku může vést část laserové energie do absorpčního zařízení, čímž se sníží výskyt odrazů. Zařízení pro dělení paprsku se obvykle skládají z optických komponent a absorbérů a výběrem vhodných komponent a úpravou rozložení zařízení lze dosáhnout nižší odrazivosti.
4. Svařovací podřez
Které procesy v procesu výroby lithiových baterií pravděpodobně způsobí podřezání? Proč dochází k podřezávání? Pojďme to analyzovat.
Podříznutí, obecně svařovací suroviny nejsou navzájem dobře kombinovány, mezera je příliš velká nebo se objevuje drážka, hloubka a šířka jsou v zásadě větší než 0,5 mm, celková délka je větší než 10 % délky svaru, popř. větší, než je standardní procesní produkt, požadovaná délka.
V celém procesu výroby lithiových baterií je pravděpodobnější, že dojde k podřezání a obecně je distribuováno v těsnícím předsvařování a svařování válcové krycí desky a těsnícím předsvařování a svařování čtvercové hliníkové krycí desky. Hlavním důvodem je, že těsnící krycí deska musí spolupracovat se skořepinou při svařování, proces přizpůsobení mezi těsnicí krycí deskou a skořepinou je náchylný k nadměrným svarovým mezerám, drážkám, zborcení atd., takže je zvláště náchylný k podříznutí .
Co tedy způsobuje podřezávání?
Pokud je rychlost svařování příliš vysoká, tekutý kov za malým otvorem směřujícím do středu svaru se nestihne znovu rozdělit, což má za následek ztuhnutí a podříznutí na obou stranách svaru. S ohledem na výše uvedenou situaci potřebujeme optimalizovat parametry svařování. Zjednodušeně řečeno, jde o opakované experimenty pro ověření různých parametrů a pokračují v provádění DOE, dokud nejsou nalezeny vhodné parametry.
2. Nadměrné mezery ve svarech, drážky, kolapsy atd. svařovacích materiálů sníží množství roztaveného kovu vyplňujícího mezery, což zvyšuje pravděpodobnost výskytu podříznutí. To je otázka vybavení a surovin. Zda svařovací suroviny splňují vstupní materiálové požadavky našeho procesu, zda přesnost zařízení odpovídá požadavkům atd. Běžnou praxí je neustále mučit a bít dodavatele a osoby odpovědné za zařízení.
3. Pokud energie na konci laserového svařování klesne příliš rychle, malý otvor se může zbortit, což má za následek místní podříznutí. Správné sladění výkonu a rychlosti může účinně zabránit tvorbě podříznutí. Jak říká staré přísloví, opakujte experimenty, ověřte různé parametry a pokračujte v DOE, dokud nenajdete ty správné parametry.
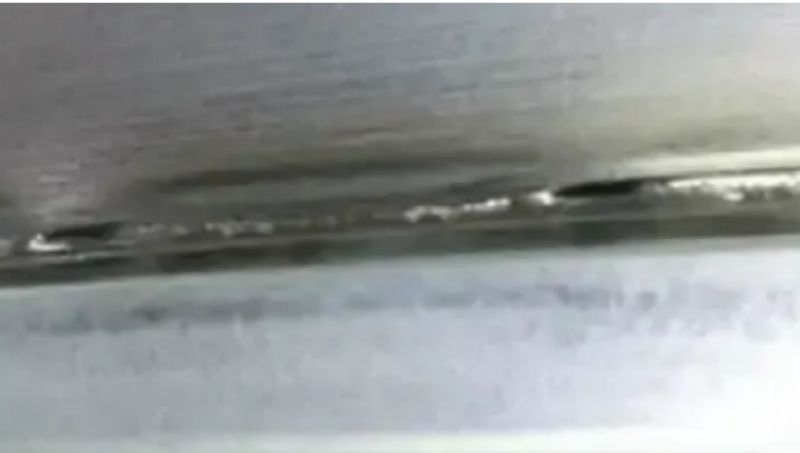
5. Zhroucení středu svaru
Pokud je rychlost svařování pomalá, bude roztavená lázeň větší a širší, čímž se zvýší množství roztaveného kovu. To může ztěžovat udržování povrchového napětí. Když se roztavený kov stane příliš těžkým, může střed svaru klesnout a vytvořit propady a důlky. V tomto případě je třeba vhodně snížit hustotu energie, aby se zabránilo kolapsu lázně taveniny.
V jiné situaci svařovací mezera pouze vytváří kolaps, aniž by způsobila perforaci. To je nepochybně problém lisování zařízení.
Správné pochopení defektů, které se mohou vyskytnout během laserového svařování, a příčin různých defektů umožňuje cílenější přístup k řešení jakýchkoli abnormálních problémů se svařováním.
6. Trhliny ve svarech
Praskliny, které se objevují při kontinuálním laserovém svařování, jsou především tepelné trhliny, jako jsou krystalové trhliny a zkapalňovací trhliny. Hlavní příčinou těchto trhlin jsou velké smršťovací síly generované svarem před jeho úplným ztuhnutím.
Existují také následující důvody pro praskliny při laserovém svařování:
1. Nerozumný návrh svaru: Nesprávný návrh geometrie a velikosti svaru může způsobit koncentraci svařovacího napětí, a tím způsobit praskliny. Řešením je optimalizace návrhu svaru, aby se zabránilo koncentraci svařovacího napětí. Můžete použít vhodné ofsetové svary, změnit tvar svaru atd.
2. Nesoulad svařovacích parametrů: Nesprávná volba svařovacích parametrů, jako je příliš vysoká rychlost svařování, příliš vysoký výkon atd., může vést k nerovnoměrným teplotním změnám v oblasti svařování, což má za následek velké napětí při svařování a praskliny. Řešením je upravit parametry svařování tak, aby odpovídaly konkrétnímu materiálu a podmínkám svařování.
3. Špatná příprava svarového povrchu: Nesprávné vyčištění a předúprava svarového povrchu před svařováním, např. odstranění oxidů, mastnoty atd., ovlivní kvalitu a pevnost svaru a snadno povede k prasklinám. Řešením je odpovídající čištění a předúprava svařovacího povrchu, aby bylo zajištěno účinné ošetření nečistot a kontaminantů v oblasti svařování.
4. Nesprávná regulace příkonu svařovacího tepla: Špatná regulace přísunu tepla při svařování, např. nadměrná teplota při svařování, nesprávná rychlost ochlazování svařovací vrstvy atd., povede ke změnám ve struktuře svařované oblasti, což má za následek vznik trhlin . Řešením je řídit teplotu a rychlost ochlazování během svařování, aby nedošlo k přehřátí a rychlému ochlazení.
5. Nedostatečné odlehčení pnutí: Nedostatečné odlehčení pnutí po svařování bude mít za následek nedostatečné odlehčení pnutí ve svařované oblasti, což snadno povede ke vzniku trhlin. Řešením je provedení vhodného odlehčení pnutí po svařování, jako je tepelné zpracování nebo vibrační zpracování (hlavní důvod).
Co se týče výrobního procesu lithiových baterií, které procesy s větší pravděpodobností způsobí praskliny?
Obecně jsou trhliny náchylné k výskytu během svařování těsnění, jako je svařování těsnění válcových ocelových plášťů nebo hliníkových plášťů, svařování těsnění čtvercových hliníkových plášťů atd. Kromě toho je během procesu balení modulu náchylné také svařování sběrače proudu k prasklinám.
Samozřejmě můžeme použít i výplňový drát, předehřev nebo jiné způsoby, jak tyto trhliny omezit nebo odstranit.
Čas odeslání: září 01-2023